Plastic Extrusion Profiles for Beginners
Wiki Article
Some Known Details About Custom Plastic Extrusions
Table of ContentsThe Custom Plastic Extrusion Manufacturers StatementsFacts About Extrusion Of Plastics UncoveredAn Unbiased View of Extruded Plastic ProfilesThe Basic Principles Of Custom Plastic Profiles
Just like any type of manufacturing procedure, the extruded account will differ somewhat during the procedure necessitating resistances on crucial dimensions. Resistances on plastic extrusions effect fit as well as function, as well as the very best time to start considering resistance requirements is throughout the initial layout phase. By dealing with Formtech early in the procedure, we can provide layout for producing assistance consisting of tolerance needs.For an extra in-depth description regarding how resistances effect rates, as well as a basic tolerance overview, please click on this link. Mass thickness is defined as the weight each volume of the plastics bought by Formtech for usage in custom-made extrusion applications. Bulk thickness effects flow as well as feed rates on the extruder, as well as variations in bulk thickness of the plastic will certainly create variations in size so it is an important consideration for custom-made extrusion production operations We spoke regarding back stress above, as well as the significance of having the ideal quantity of back pressure throughout the extrusion process for physical home control (plastic extrusion profiles).
As soon as the plastic compound departures the extrusion pass away in a pressed kind, the substance will certainly relax, or expand somewhat. This is described as die swell. Die swell is material particular, indicating for example a vinyl (PVC) material will experience a various die swell than a Polyethylene or Polypropylene substance.
In the extrusion process cleaning materials out of barrels, screws as well as plastic extrusion tooling takes some time as well as raises cost (https://www.pageorama.com/?p=k3ll3rpl4st8). If product adjustments are being made on the line from one job to the following, this can involve getting rid of and cleansing the die, drawing the screw on the equipment to tidy, and brushing out the barrel of the machine while the screws are out.
How Plastic Extruded Profiles can Save You Time, Stress, and Money.
The removing materials are so stable they can even be left in the extrusion die throughout storage space, placed back on the extruder the next time the work requires to run, and started without time consuming cleaning. The regular compound will push the cleanup out of the die when it departures.

There are actually 2 techniques that can be pop over here utilized to achieve this feeding process - https://hub.docker.com/u/k3ll3rpl4st8. First, the material can be had in a hopper directly above the feed-throat of the extruder and also fed by gravity. The screws will then absorb the optimum quantity of product they can with every revolution of the device, as well as this is called flooding feeding.
The flights of the screw are not entirely full of every transformation of the equipment. This is called starve feeding of the extruder, and provides some benefits to the extrusion professional in specific circumstances. By not loading the screw channel completely, it provides more control to the service technician, as well as gets rid of a few other variables that can accompany flood feeding.
Custom Plastic Extrusions - Questions
For every change of a single screw machine, there is some slippage back over the trips of the screw. This slippage is beneficial for blending of products as well as colorants, but it produces an opportunity for some rising as well as variant with the screw transformation. With this holding true, varying stress as product comes off the screw can trigger this processing problem for the extrusion technician.Call today or e-mail at [email safeguarded] to learn more.
Such a variety of products as well as makes use of represents the wide range of suitable products and also flexibility that the extrusion process pays for in developing custom-made accounts to fulfill your exact specs. The plastic profiles produced in the extrusion procedure can be either adaptable or rigid. Both deal benefits for various usage cases (https://www.tripadvisor.in/Profile/k3ll3rpl4st8).
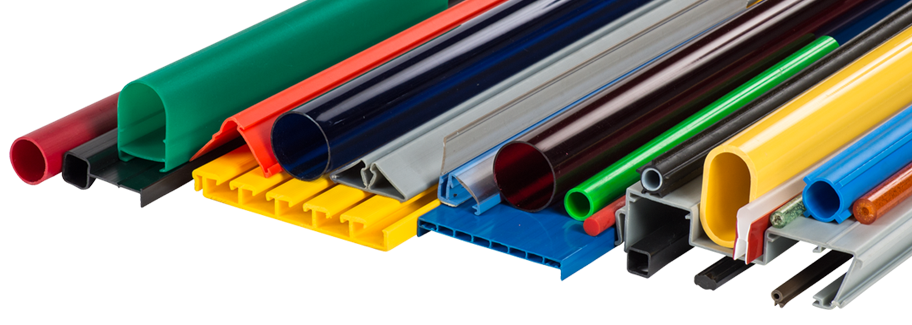
Custom Plastic Extrusions for Beginners
While it eventually never ever prospered at its desired function, it however found routine usage in the automobile field in other methods, many thanks to its high fluid resistance and also outstanding securing efficiency. Automotive parts frequently made from Santoprene consist of weather seals, bumpers, cord jacketing, and also a lot more. Santoprene TPV's remarkable securing residential property also makes it particularly beneficial in building and construction, where it can be used to make window seals, tubes, electric adapters, and caster wheels (custom extrusion manufacturer).We utilize sophisticated technology in order to create the exact kind of extruded product you need. We are thrilled to start dealing with you soon!.
Manufacturing high quality products is as crucial to us as attaining the highest possible standards for customer care. At the forefront of our solution are specialist and also committed staff members that fulfill day-to-day obstacles with cutting-edge suggestions - extrusion of plastics. Consumer email Customized profiles/ forms Twin Products Hollows Rods Tubes Angles Bindings Brackets Caps Stations Clips Edgings Insulators J-Retainers/ J-Clips Moldings Retainers Seals Sleeves Spacers Straps T-moldings Tapes Tracks Cold Temperature Efficiency Shade Matched Dual-Durometer Simplicity of Setting Up Embossed Flame Retardant Flexible High Gloss Heat Efficiency Interlocking Locking Matte Non-Contact Food Grade Ribbed Snap Fit Stiff Toughness Distinctive Weatherability Aerospace Appliance Air/Water/Pollution Control Automotive Structure Products Concrete Building And Construction Electrical Lawn & Yard Logistics/ Transport Marine Office Systems Factor of Purchase (POP) Display Several Solutions Can Be Dealt With In-Line to Eliminate Second Workflow Adhesive/Transfer Tape Application Cut to Size Reducing Drilling Embossing Warmth Sealing Laminating Punching Directing Slotting Special Packaging Welding AIAG Automotive Market Action Team ASME American Society of Mechanical Designers ASTM American Society for Screening as well as Products DOT Department of Transport FDA Fda FMVSS Federal Automobile Safety Standards MIL-STD Armed Force Specifications SAE Culture of Automotive Engineers UL Underwriters Laboratories ISO International Organization for Standardization.
Report this wiki page